Utah Valley Hospital is the only Level II trauma center between Salt Lake City and St. George. With the population in the region expected to double by 2030, improvements in efficiency, technology, and seismic stability were critical. Initially founded in 1939, the hospital had outlived multiple expansion projects and needed more coherency. The campus desperately needed seismic and technological upgrades.
THE GOAL
Critical to the community, the hospital needed to remain fully operational throughout construction. The engineering staff at Reaveley assisted Intermountain in fulfilling its mission to "help people live the healthiest lives possible." Intermountain's first "fundamental of extraordinary care" is safety. The physical hospital facility is the first measure of safety patients approach and the last before their departure. The building ensures patients and caregivers are safe.
THE CHALLENGE
The typical large hospital sees an average of 3,800 trips per shift. Any structural elements interfering with a given route could hamper the staff's ability to provide optimal safety and care. The monumental task of keeping the facility operational required 26 phases of construction, which allowed shifting and relocation of hospital functions while existing buildings were demolished and new facilities were built. In all, the project replaced more than half of the existing hospital. The tunnel remained in place as the new 12-story hospital tower, and supporting foundations were built over and around it.
"Before the project, as hospital services grew and expanded, needed services were patchworked into the existing campus wherever space was available," said Josh Rohatinsky, Intermountain Health's administrative director. "This project corrected those inefficiencies not only for the needs of today but also for the future. Service line geographies have been consolidated, the patient flow has improved dramatically, and standardization initiatives such as supply storage in decentralized nurse servers and other locations have allowed our clinical staff to spend more time with their patients."
In addition to above-ground complexities, liquefaction's significant hazard caused the existing foundations to settle an estimated 8 inches. There is also potential for future liquefaction settlement to occur in the event of a major earthquake. The new design mitigates future liquefaction with deep soil mixing and a combination of mat foundations and spread footings tied together with grade beams. Deep soil mixing resulted in a 35-foot-deep grid of 7-foot diameter shafts wherein cement grout mixed with soil in place as the auger was drilled. This solution was deemed the most economical compared with rammed aggregate piers, auger cast piles, drilled piers, driven piles, or over-excavation and replacement.
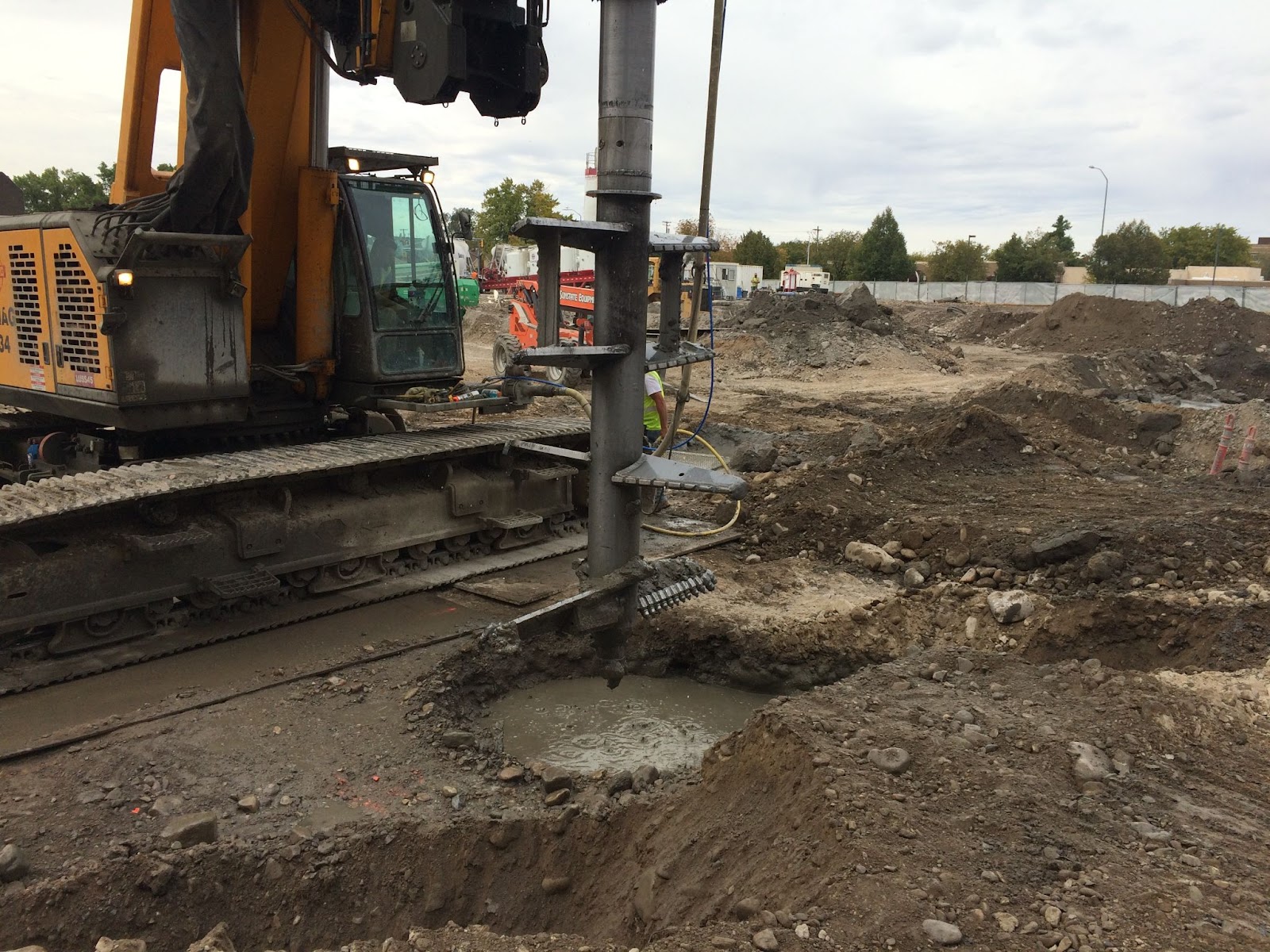
During construction, Reaveley and Jacobsen Construction regularly measured and monitored foundation settlement throughout project construction. These measurements showed the maximum settlement to be 1.08 inches (the average settlement was 0.4"), less than the 2-inch tolerance.
SOCIAL, ECONOMIC, AND SUSTAINABLE DESIGN CONSIDERATIONS
Schedule and budget are at the forefront of every client's mind, and Intermountain is no different. However, Intermountain values the physical facility as another tool to offer its patients "extraordinary" care. The design team worked tirelessly to devise the most cost-effective structural system while issuing early bid packages to achieve Intermountain's schedule goals.
The foundation system saved the project roughly $3.5M while improving the settlement performance. Monitoring has demonstrated settlement at less than half of the acceptable tolerance.
Owners, engineers, architects, and contractors involved in the design and building of modern healthcare facilities also understand the role of the physical facility on staff and patient safety, understanding that the building is an essential tool in the caregiving process. The hospital's design, with its equipment and technology, enhances patients' quality and safety by improving how their facilities address patient and staff safety. The spatial configuration of the hospital caregivers' units includes patient rooms, nurses' areas, corridors, and specialized areas such as storage and supply rooms. The structure must hold these spaces intact without impeding the paths of caregivers from one point to another. A moment frame system was selected over a braced frame system to keep the floor plan open and provide ultimate flexibility in the use of the space and in future modifications.
Improvements to the physical environment in which nurses and other caregivers work will improve outcomes for caregivers and patients for decades to come.
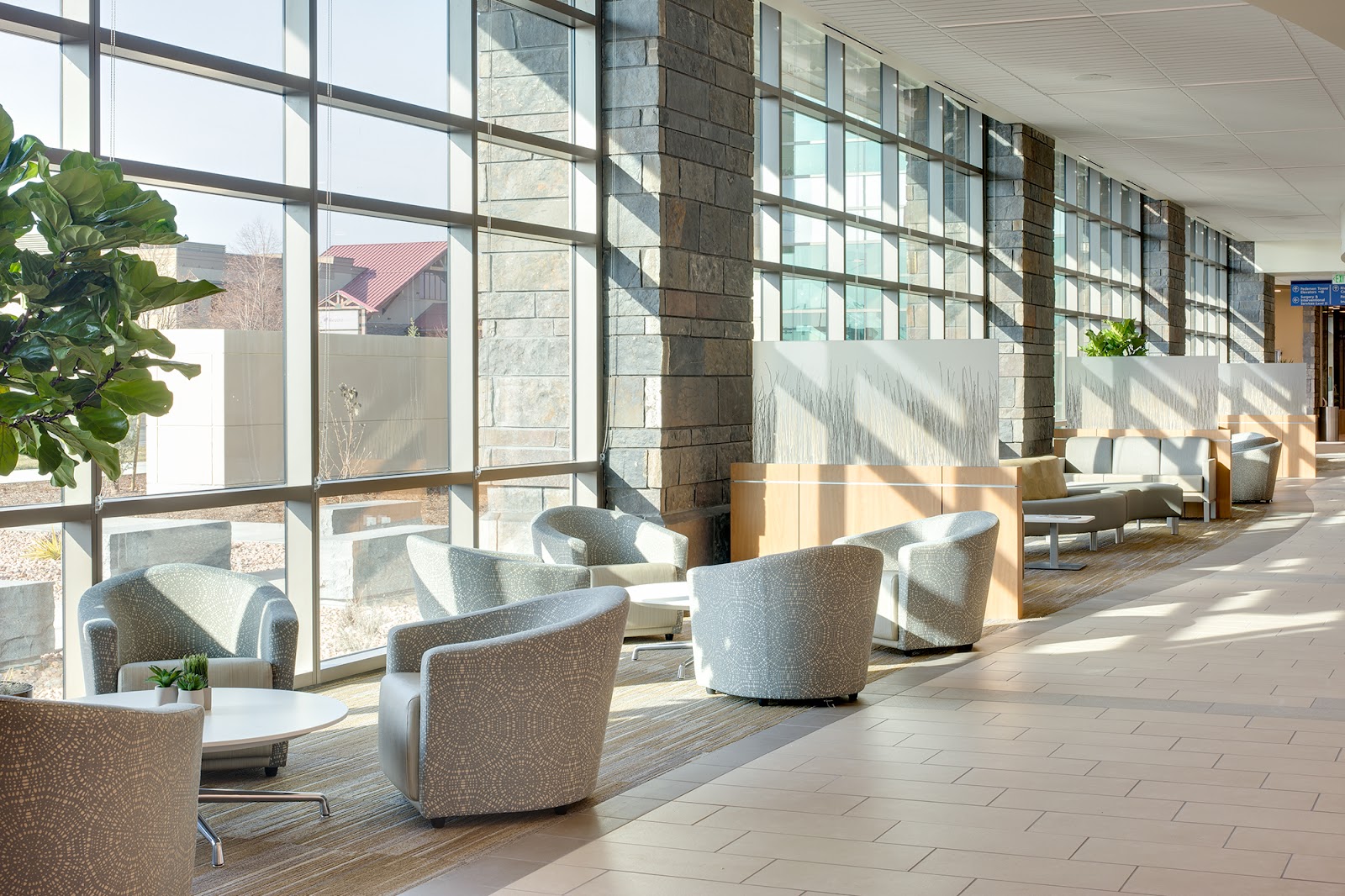
General Contractor: Jacobsen Construction
Architect: HDR Architecture
Associate Architect: NJRA Architects
Mechanical Engineer: Van Boerum & Frank Associates
Electrical Engineer: Spectrum Engineers
Civil Engineer: Great Basin Engineering, Inc.
Landscape Engineer: Arcsitio Design