The new correctional facility in Salt Lake City accommodates modern programs and services to help reduce Utah's 46% recidivism rate and decrease long-term incarceration growth. The State of Utah Department of Corrections observed that 67% of all prison admissions were parole and probation violators. Better preparing offenders for release reduces this number, which is higher than the national average.
THE GOAL
The state sought to provide better-designed space for substance abuse treatment, mental health counseling, sex offender treatment, and training and education. The new correctional facility benefits society by helping to build safer communities, establish a fairer criminal justice system, and rehabilitate repeat offenders while teaching them the skills that will help them become productive, tax-paying citizens.
A team of local and national experts worked with the State of Utah to realize its vision, beginning the new facility's design in 2015. The new Utah State Correctional Facility (USCF), located nine miles west of Salt Lake City International Airport, comprises 35 buildings and over 1.35 million square feet of space. The facility, which can house up to 3,600 inmates, was built to improve inmate and staff experience. The design team focused on developing a modern facility offering inmates a more comprehensive array of services and opportunities to help them reenter society with a better chance of success in our local communities. At the center was a push to provide ample natural light to improve the mental health of the facility's occupants including staff, inmates, and the visiting public. According to a press release by the governor's office, "the driving factors in determining the concepts for design for the USCF were direct supervision, increased daylight for both incarcerated individuals and staff, uncompromised security and safety for both, and normalization of life for incarcerated individuals to aid them in reentering society."
The complex includes separate buildings for the various needs of the Department of Corrections, including housing for general male and female populations, maximum security, substance abusers and sex offenders, mental and medical health, food services, exercise facilities, administration, warehouse space, and other supporting services. While a mixture of building material types was used, most buildings utilized tilt-up concrete wall construction. The housing units utilized precast concrete cells with some reinforced masonry partitions.
THE CHALLENGE
According to the Utah Division of Facilities and Construction Management (DFCM), the project constitutes the largest construction project in the state's history. It was a joint venture between Layton Construction and Okland Construction (LOJV) and required the contribution of multiple architectural and engineering firms to achieve the aggressive time frame. Reaveley was one of four structural engineering firms working on the project in a collaborative effort. However, as the coordinating structural engineer, we were responsible for standardizing the structural engineering approach across the site, including creating a standard set of structural notes and details used project-wide.
Among the project's many unique challenges included a building site with extremely poor soils and an overall corrosive environment.
The facility sits on a site with deep and soft soils highly susceptible to short and long-term settlements. Reaveley worked with Gerhart Cole, a geotechnical consultant, to explore options for addressing soil issues. The use of aggregate piers was investigated and is a typical means to mitigate settlement problems, but the site's sheer size made the approach cost-prohibitive. Other deep foundation systems posed the same drawback. The team then considered using an approach widely used in transportation-type projects but not typical for buildings–pre-consolidating the soils. Wick drains and overburden were placed at the locations of each building's pad. The site saw settlements of over 12 inches in the first several months following the placement of the overburden. We then designed the mat and other footings to keep soil stresses low. Several years after constructing the first building, there were no settlement issues.
Both the air and the soil on the site are highly corrosive. Working with a corrosion consultant, we devised a strategy for dealing with these issues and achieving the 75-year life required by the owner. Concrete tilt-up sandwich panels allowed for continuous insulation at the building envelope and provided durable exterior and interior surfaces. For the most part, steel was eliminated from the exterior, reducing the potential for corrosion. Corrosion inhibitors and epoxy-coated rebar were the ideal solutions for steel reinforcement throughout the site, including at the exterior corners and interface of the footings and soils.
However, corrosion inhibitors make it very difficult to finish the concrete. At locations where the mat footings were also serving as the polished cell floors, Reaveley devised a strategy for getting the inhibitor where it was needed while minimizing it where the floors required a high-quality finish. This approach required a staged construction for the mat footings.
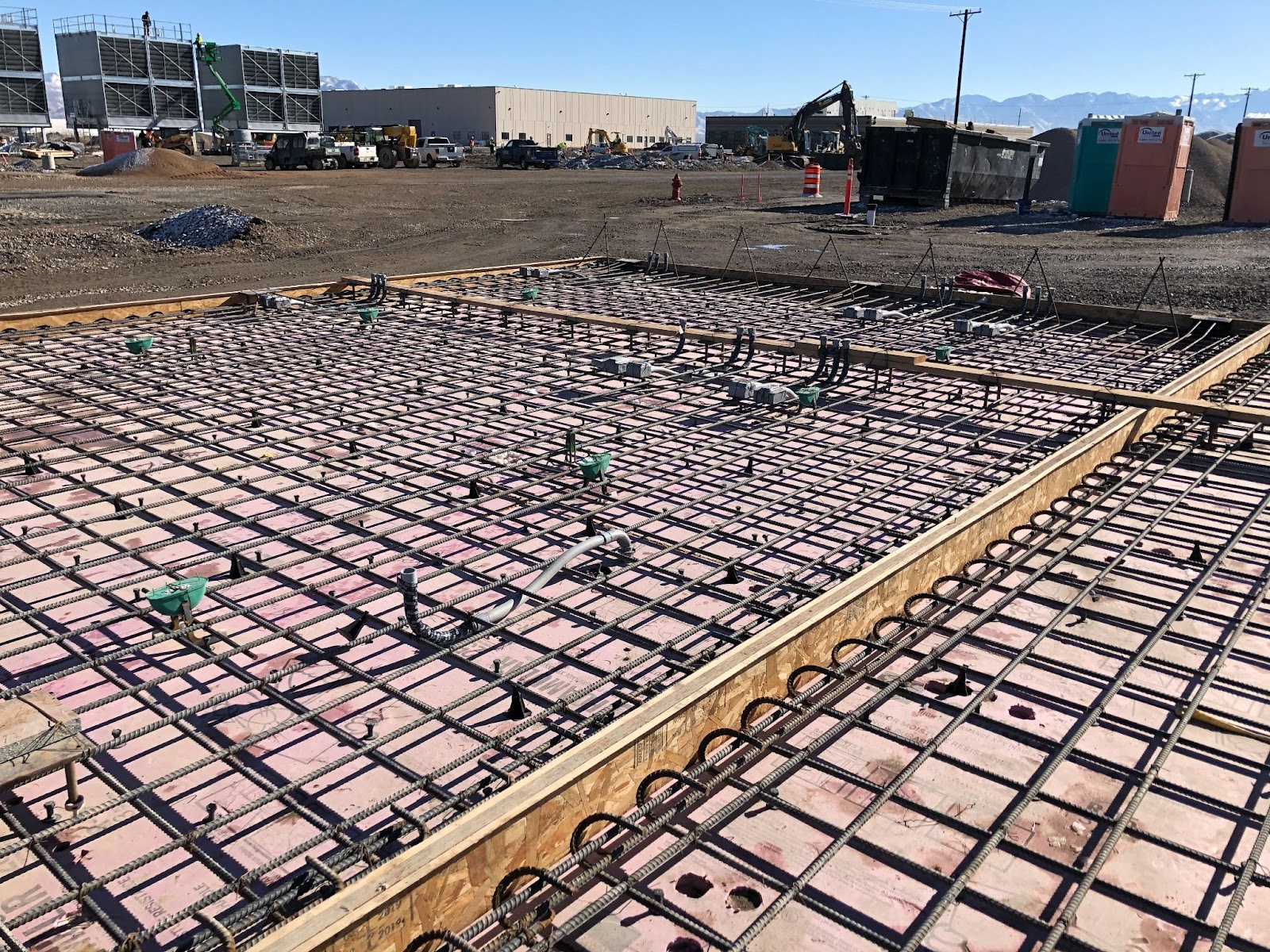
Of significant concern for the owner was the inclusion of high-quality and durable cells for the inmates. Keeping costs at a minimum was a high priority. A cost study looked at various options, and the team selected precast concrete cells throughout the facility. Our team piloted a strategy to let the cells serve as gravity and lateral load-carrying elements to efficiently implement these cells in the buildings and keep costs down. The system required focused coordination among the design team and two separate precast concrete suppliers. The result was tilt-up walls designed by Reaveley, precast cells provided by one supplier, and intermediate support walls provided by a second supplier. Engineering a facility that could rely on each of the three components for earthquake resistance eliminated the need for costly and unnecessary redundancy.
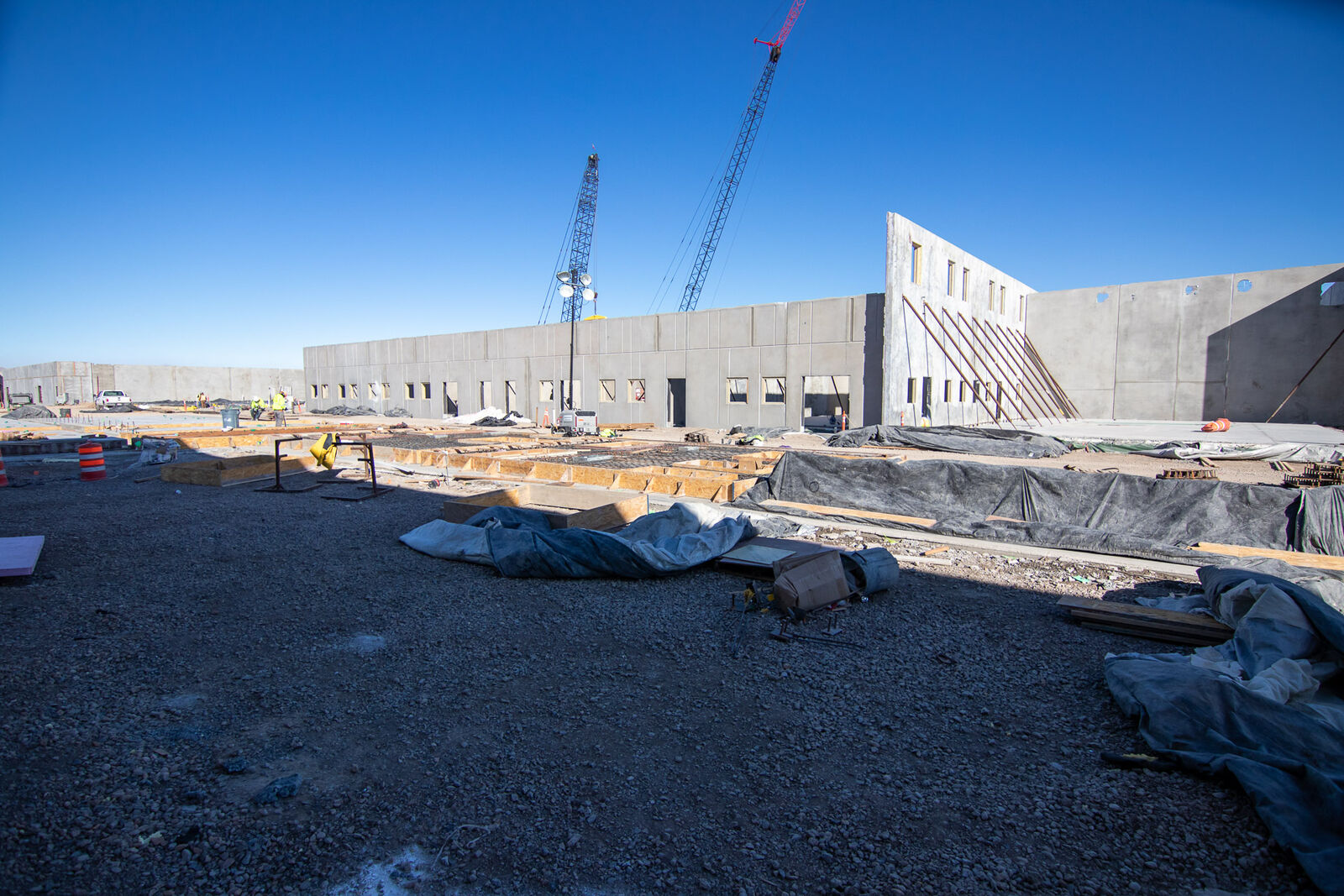
SOCIAL, ECONOMIC, AND SUSTAINABLE DESIGN CONSIDERATIONS
The most sustainable designs are those that don't require a rebuild following a significant seismic event. By code, the majority of the buildings on this project were classified as risk category III. For seismic considerations, Reaveley recommended elevating the seismic hazard to an equivalent risk category IV to improve the likelihood that the buildings could be used for the inmates and staff to shelter in place following a significant seismic event.
The male maximum security building was structurally complete when the 2020 Magna earthquake struck Salt Lake Valley. A recording station near the new facility suggests that the ground accelerations at the new site may have met or exceeded the design thresholds. However, the building performed well and only manifested a few cracks in some architectural panels.
The project budget was a primary concern and was at the forefront of the design process. Our ability to marry two different precast concrete systems with a tilt-up concrete building resulted in tremendous cost savings. We designed the precast cells to serve a dual purpose in the building function: 1) provide the functionality of a cell and 2) provide structural support and stability for the building.
In the end, Reaveley Engineers and the rest of the design and construction team rose to the challenge of this monumental and complicated project by leveraging our experience and innovative thinking to tackle various obstacles and meet the owner's objectives. Through collaboration and innovation, the team delivered a facility that met the state's functional needs for a safe, bright, and effective correctional facility. Although the overall project budget increased during construction due to the pandemic, labor shortages, and material shortages, actions taken by Reaveley and the rest of the design team early in the process saved money overall.
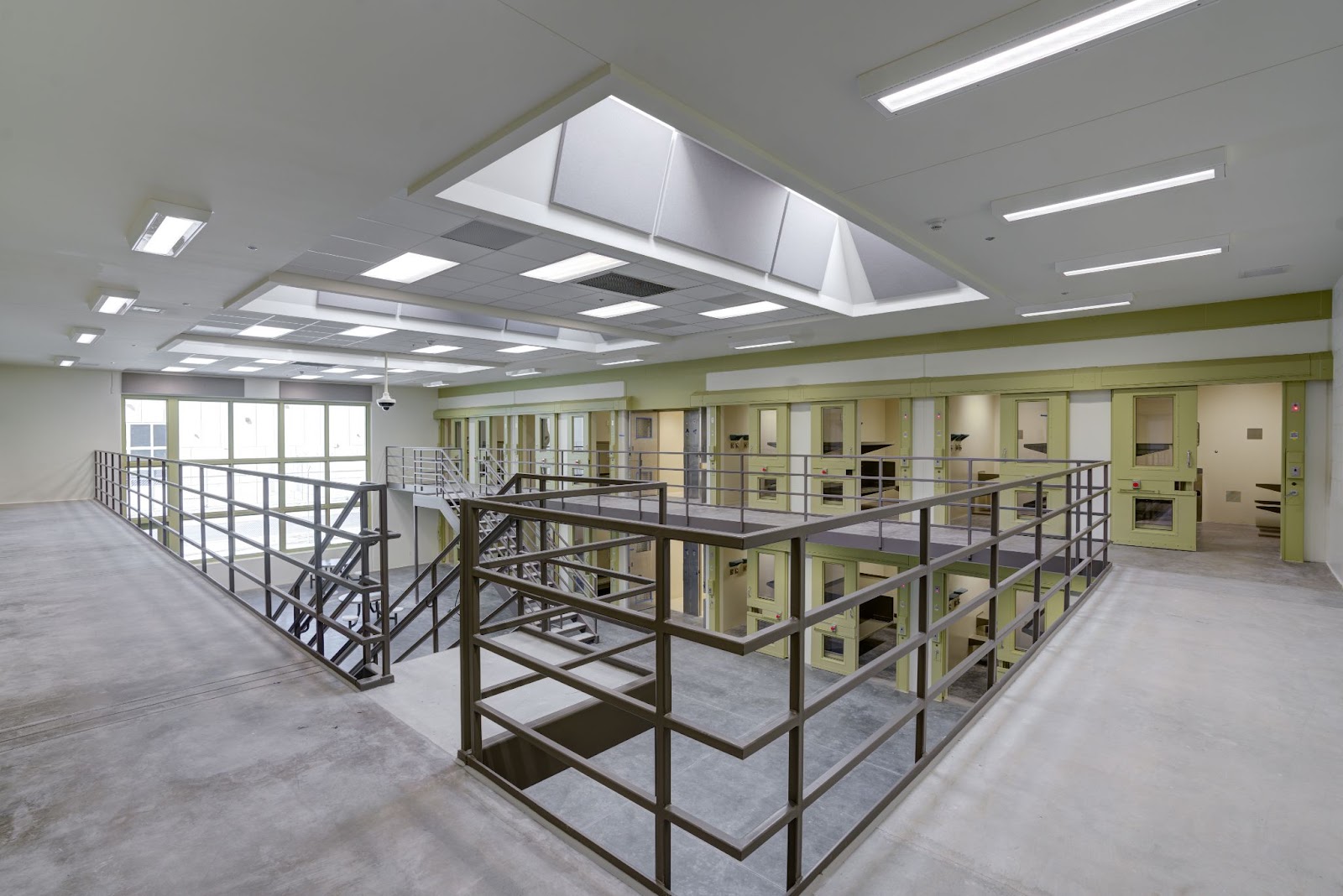
Coordinating Structural Engineer: Reaveley Engineers
Additional Structural Engineers: HOK Group, Inc., Dunn Associates, Inc., and HKS, Inc.
General Contractor: LOJV (JV between Layton and Okland)
Architect: HOK Group, Inc. and GSBS Architects
Geotechnical Engineer: Gerhart Cole, Inc.
Mechanical Engineer: HOK Group, Inc.
Electrical Engineer: Spectrum Engineers
Civil Engineer: PSOMAS
Detention Consultant: HOK Group, Inc.
Precast Concrete: Oldcastle Precast and Olympus Precast
Commissioning: Bernhard